As the new home of the Las Vegas Raiders football team, Allegiant Stadium is an iconic addition to the Las Vegas strip. With 65,000 seats that can be expanded by 7,000 additional seats during major events, it is the largest entertainment venue in Las Vegas. The stadium is expected to generate $62 million of economic benefits annually while creating 6,000 permanent jobs in the city.
Arup, in partnership with architect of record HNTB, design architect Manica Architecture, project manager CAA Icon, and Mortensen & McCarthy Joint Venture (MMcJV), helped bring the unique stadium to life, providing structural and façade engineering as well as building maintenance for the project.
Allegiant Stadium will be used for a variety of events beyond Raiders football games, and it has been designed to be flexible so that it can be adapted for everything from professional and college football games to non-sporting events such as concerts. It features walls that open to views of the Las Vegas Strip, as well as a translucent cable-truss supported roof.
To achieve the architectural design, Arup incorporated a lightweight and delicate cable truss roof. This type of structure is unusual in the United States, and normally requires significantly more precise construction tolerances and methods to achieve. Typically, the entire steel compression ring structure is built and test-fitted offsite to ensure the tight tolerances required for the cables are met, then disassembled and shipped to the project site. This adds cost and time to the construction schedule due to multiple iterations where the steel is assembled and disassembled as it is adjusted to fit.
To save time and money, Arup implemented a unique design using 54 field adjustable nodes. These nodes could be adjusted to the right tolerance at the interface to the cable structure – all without impacting the fabrication and erection of the steel canopy. Multiple surveys of the steel canopy at the end of fit-up and erection ensured that each node was properly adjusted to within 25mm of its required position prior to the cable big lift. Then the cables, which had been precisely cut to length months earlier in Switzerland and shipped to Las Vegas without any splices, were rolled out onto the field, lifted, and prestressed into position to support the transparent inflated ETFE (Ethylene Tetrafluoro-ethylene) pillow roof.
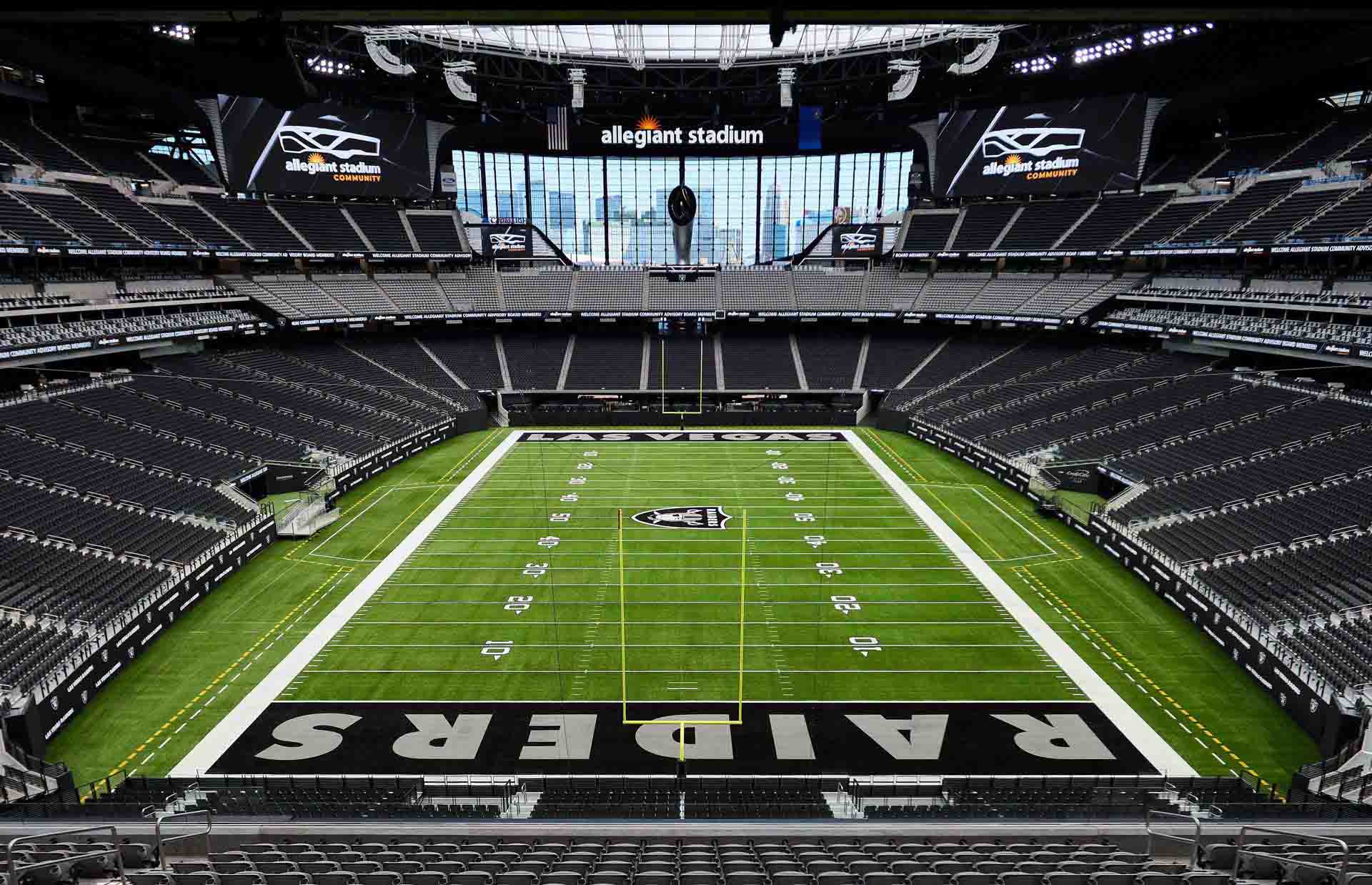
From concept design to completion in only 40 months, Allegiant Stadium is the fastest designed and constructed US football stadium of its size. The fast-track Design-Build delivery method was essential in completing the stadium on budget and on time for the start of the 2020-21 football season. Working together with the Clark County Department of Building and Fire Prevention, the Arup team implemented a collaborative review and permitting approach to allow MMCJV to start work on the foundations and concrete bowl structure four months prior to permitting the steel and cable structure above.
At the same time, Arup issued an early steel mill order and detailing sequences to the steel fabricator to ensure the structural steel was ready on site to start erection the day the final structural permit was pulled. Arup created the structural steel design model in Tekla, the industry standard fabrication model software, to allow the project team to collaborate and share BIM content directly with the builder with no missed translations as designs moved between platforms. In addition, Arup’s digital team created automated tools to regularly convert the Tekla model into a native Revit model for cloud collaboration with the rest of the design team.
From concept design to completion in only 40 months, Allegiant Stadium is the fastest designed and constructed US football stadium of its size. The fast-track Design-Build delivery method was essential in completing the stadium on budget and on time for the start of the 2020-21 football season. Working together with the Clark County Department of Building and Fire Prevention, the Arup team implemented a collaborative review and permitting approach to allow MMCJV to start work on the foundations and concrete bowl structure four months prior to permitting the steel and cable structure above.
At the same time, Arup issued an early steel mill order and detailing sequences to the steel fabricator to ensure the structural steel was ready on site to start erection the day the final structural permit was pulled. Arup created the structural steel design model in Tekla, the industry standard fabrication model software, to allow the project team to collaborate and share BIM content directly with the builder with no missed translations as designs moved between platforms. In addition, Arup’s digital team created automated tools to regularly convert the Tekla model into a native Revit model for cloud collaboration with the rest of the design team.
From concept design to completion in only 40 months, Allegiant Stadium is the fastest designed and constructed US football stadium of its size. The fast-track Design-Build delivery method was essential in completing the stadium on budget and on time for the start of the 2020-21 football season. Working together with the Clark County Department of Building and Fire Prevention, the Arup team implemented a collaborative review and permitting approach to allow MMCJV to start work on the foundations and concrete bowl structure four months prior to permitting the steel and cable structure above.
At the same time, Arup issued an early steel mill order and detailing sequences to the steel fabricator to ensure the structural steel was ready on site to start erection the day the final structural permit was pulled. Arup created the structural steel design model in Tekla, the industry standard fabrication model software, to allow the project team to collaborate and share BIM content directly with the builder with no missed translations as designs moved between platforms. In addition, Arup’s digital team created automated tools to regularly convert the Tekla model into a native Revit model for cloud collaboration with the rest of the design team.